Vážení zákazníci, radi by sme vás informovali, že naša firma bude zatvorená v dňoch 14. – 18. júla 2025 z dôvodu celofiremnej dovolenky.
Objednávky a dopyty prijaté počas tohto obdobia budú spracované a expedované v pondelok 21. júla 2025.
Ďakujeme za pochopenie.
Ktorý typ montáže T-spojov víťazí?
01.01.1970Porovnali sme tri metódy tvarovania odbočiek
V dnešnej dobe bude každý súhlasiť s tým, že v priemysle sú primárnymi cieľmi kvalita v širšom zmysle slova a produktivita. V odvetviach, kde sa kladie veľký dôraz na čistotu, ako napríklad v potravinárskom, farmaceutickom a kozmetickom priemysle - sa kilometre potrubí používajú okrem iného na rozvodné slučky plynov a kvapalín, čistiace systémy ako CIP (z angl. Clean In Place) a SIP, (z angl. Steam In Place), filtračné systémy alebo výmenníky tepla atď.
Všetky tieto siete si vyžadujú rozdeľovacie potrubie. Zmienka o potrubiach tiež znamená zmienka o T-spojoch. Tieto rozdeľovače sú zvyčajne vyrobené z nehrdzavejúcej ocele podľa odporúčaní smernice EHEDG č. 8- „Stavebné materiály musia byť antikorózne, netoxické, mechanicky stabilné a ich povrchová úprava nesmie byť nepriaznivo ovplyvnená za podmienok určovaného použitia“ a štandardu ASME BPE, ktorý obhajuje použitie nehrdzavejúcej ocele radu 300, presnejšie 316L. Pre hygienické aplikácie je nehrdzavejúca oceľ 316L čistiteľná, tvarovateľná za studena a obsahuje 2 až 3% molybdénu, čo výrazne zvyšuje jeho odolnosť proti korózii.
Existujú tri hlavné metódy tvarovania odbočiek:
- Inštalácia potrubí na otvory vyvŕtané v potrubí (obr. 1 a 2)
- Inštalácia T-spojov na dĺžky potrubí (obr. 3)
- Vytvorenie odbočných spojov priamo z vedeného potrubia (Extrudované hrdlo - metóda T-DRILL) (obr. 4)
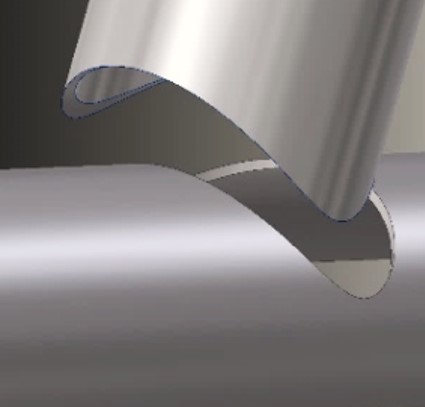
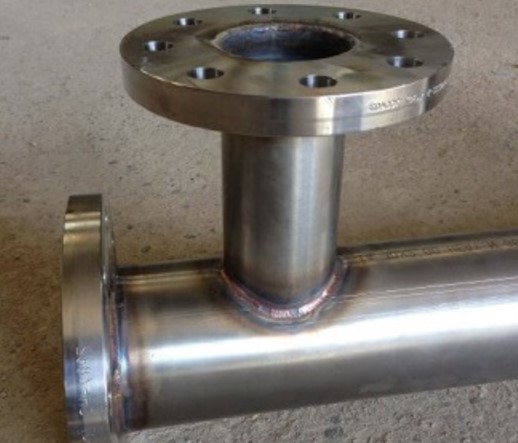
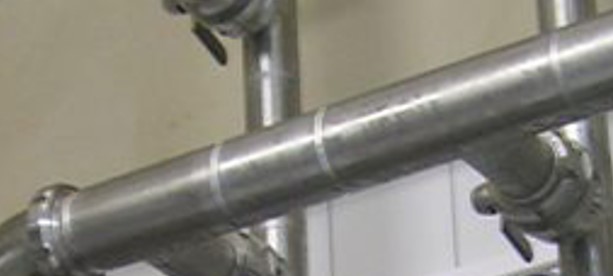
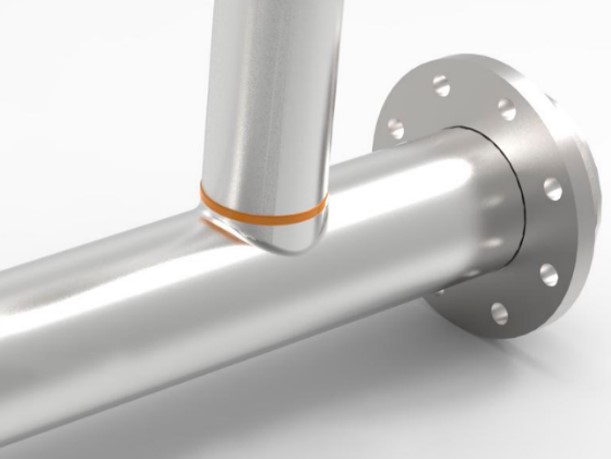
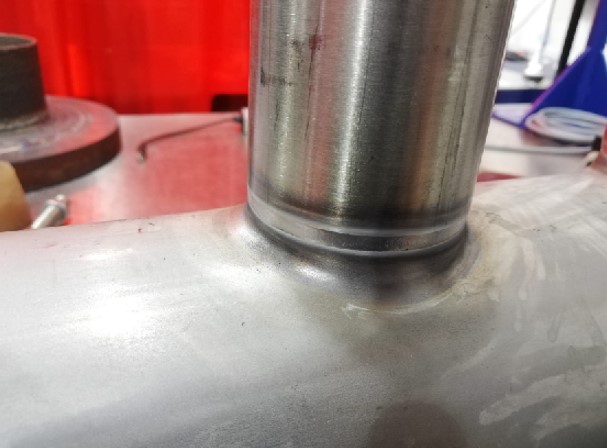
Pri rúrkach s hrúbkou až 12,7 mm je najlepší a najefektívnejší spôsob výroby týchto rozdeľovačov mechanické (T-DRILL) vytvorenie odbočných spojov priamo na vedenom potrubí. To minimalizuje potrebu zvárania a možné miesta netesností alebo miesta náchylné na zachytávanie kontaminantov. Ak je potrebné dodatočné leštenie rúrok vo zvarených bodoch, je to účinnejšie pri mechanicky vytvorenom odbočnom spojení, pretože existuje minimálne množstvo tupo zváraných a dokonale kolmých spojov.
V oblasti inštalácie potrubí nad otvorom existujú takzvané spojenia „Fish-mouth connection“ (obr. 2).
Napriek tomu, že spojenie „rybie ústa“ je veľmi dlho používanou metódou, v dnešnej dobe predstavuje najväčšie riziko z hľadiska hygieny. Tvar je skutočne zložitý, pokiaľ ide o zváranie, a z dôvodu produktivity sa často používa ručné zváranie. Táto metóda, dokonca ani pri najlepšej ručnej zváračke, nemôže zaručiť hladký a čistý zvar v najkomplikovanejších oblastiach. Tento tvar navyše predstavuje oblasti, v ktorých je čistenie takmer nemožné.
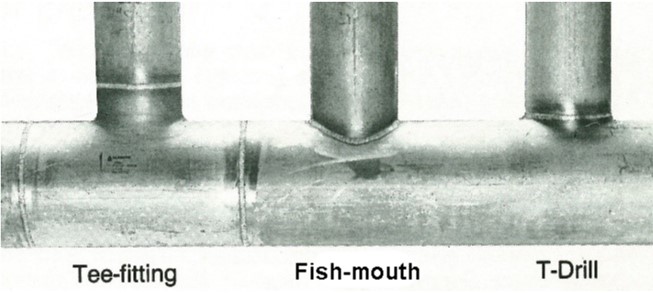
Pokiaľ je to možné, jedna z najefektívnejších metód spočíva v eliptickom frézovaní otvorov, mechanickom vytláčaní alebo tvarovaní (lemovaní) spoja vetiev a orezávaní povrchu vytlačenej časti, a to všetko bez toho, aby bolo potrebné pohybovať rúrkou. Po mnohých rokoch sa uznáva, že automatické orbitálne zváranie je najvhodnejším riešením pre montáž vzhľadom na kvalitu výsledku, zisky vo výrobe a skutočnosť, že spĺňa všetky požiadavky vysokej čistoty.
Porovnanie T-Drill metody s bežným zváraním fitingov:
Ďalším bežným aspektom týchto odvetví je, že ich systémy sú vyrábané z leštenej austenitickej rúrky z nehrdzavejúcej ocele, spravidla zostavenej autogénnym zváraním na tupo alebo fúziou. Pri správnom vykonaní a pri podobnom obsahu síry v prvkoch, tento typ zvaru vytvára vysoko pevný spoj bez prasklín alebo pórovitosti, ktoré by mohli zachytávať prvky náchylné na následnú kontamináciu výrobku. V oblasti ultra-vysokej čistoty môže byť kvôli optimalizácií toku vykonaný elektrolytický leštič.
Pre správnu montáž sa musí vziať do úvahy tiež množstvo charakteristických vlastností, ktoré sú spojené s vyhotovením týchto rozdeľovačov s extrudovanými otvormi. Mechanické vytváranie vetvového spojenia systematicky zahŕňa veľmi miernu ovalizáciu, ktorá musí byť vždy zahrnutá v normalizovaných hodnotách orbitálneho zvárania.
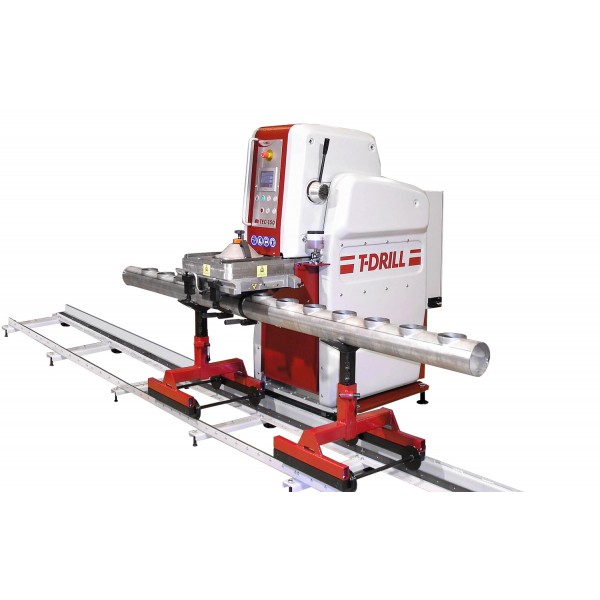
Extrúzia tiež zahŕňa určité zúženi hrúbky mechanicky vytvorenej odbočky; v závislosti od pomeru medzi priemerom vetvy a priemerom rozdeľovača. S vedomím, že čím sú priemery trubice a odbočnej trubice podobnejšie, tým dôležitejšie je zriedenie steny, na optimalizáciu výsledku zostavy sa spravidla používa pomer blízky 2.
Výška takto vytvorených hrdiel je daná použitým materiálom, jeho predĺžením a rozmermi/pomerom rozchodových a odbočných rúrok. Výška hrdla sa obvykle pohybuje medzi 2 a 20 mm medzi malými a veľkými rozmermi potrubia. Táto výška je samozrejme zmenená orezaním, aby bola zaistená optimálna kontaktná plocha s odbočnou rúrkou. Výškou mechanicky tvarovaného hrdla je úplne možné vykonať montáž orbitálnym zváraním TIG.
Výška hrdla samozrejme znamená, že v určitých prípadoch by mala zváracia hlava obsahovať systém, ktorý elektródu nakloní alebo zošikmí, aby sa umiestnil v oblasti, ktorá sa má zvárať, a zaistí účinný plynový štít, kvôli zabráneniu akejkoľvek oxidácii. Podľa typu použitých hláv bude plynový štít buď v uzavretom priestore (obr. 7) alebo difúziou (obr. 8).
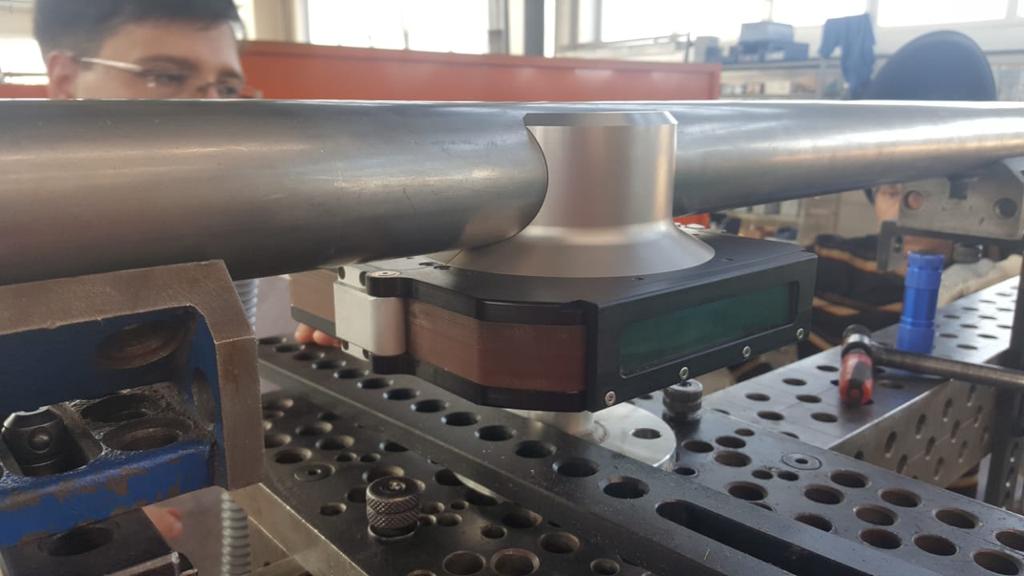
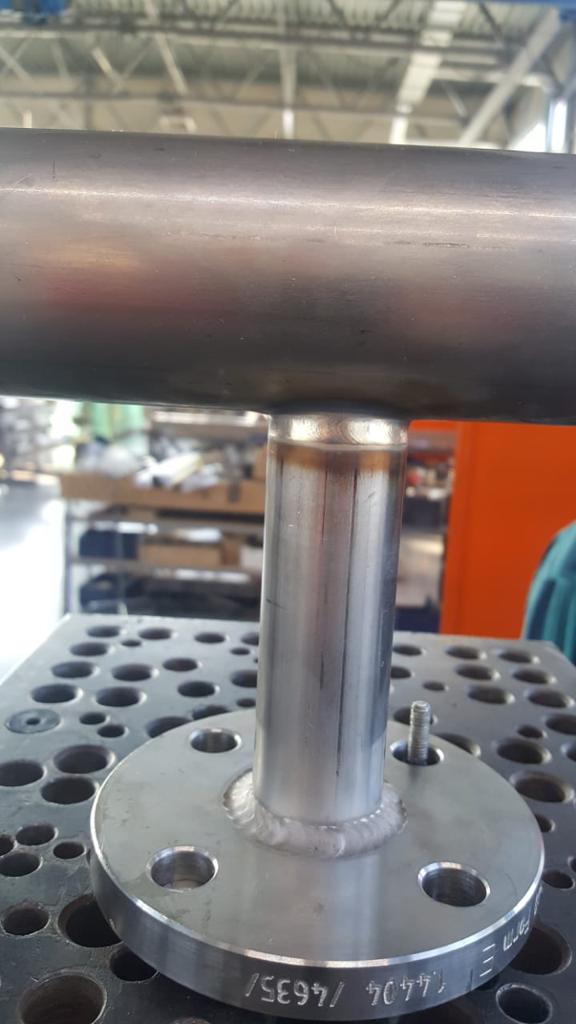
Evidentne bude ďalším preventívnym opatrením, bez ohľadu na typ hlavy, zavedenie plynového systému na druhej strane, aby sa zabránilo akejkoľvek oxidácii vnútorného zvaru.
V dnešnej dobe sú zváracie generátory vybavené dialógovými systémami, ktoré umožňujú výber najlepšej prevádzkovej metódy podľa rôznych parametrov, ako sú použité priemery, materiály atď. Asistované programovanie podporuje kvalitu zvaru. Rozdelenie na oblasti zvárania uľahčuje zvládnutie zvarového kúpeľa v každom ohľade, presnejšie jeho polohu, hrúbku a tvar v spoji.
Na záver možno povedať, že technické objavy a technologické inovácie v ovládaní zváracích materiálov a postupov v súčasnej dobe zaručujú kvalitu výrobkov a inštalácií a zároveň zlepšujú produktivitu. Mechanické tvarovanie hrdiel na rozdeľovačoch minimalizuje počet sekundárnych zvarov a operácií, znižuje množstvo zakúpených T-spojov a je dokonale kompatibilné s orbitálnym zváracím zariadením TIG, čím je zaistená úplná bezpečnosť opakovateľnosti zvaru.
Poraďte sa s našími odborníkmi
Chcete vidieť stroje na vlastné oči alebo sa o strojoch T-Drill dozvedieť viac? Neváhajte nás kontaktovať. Stroje vám radi osobne predstavíme.